Cold Drawing Process
Cold drawing is the process of drawing materials at room temperature. During the drawing process, the material passes through the die. Through the extrusion of the material by the die, the diameter of the material can be changed according to the different sizes of the die.
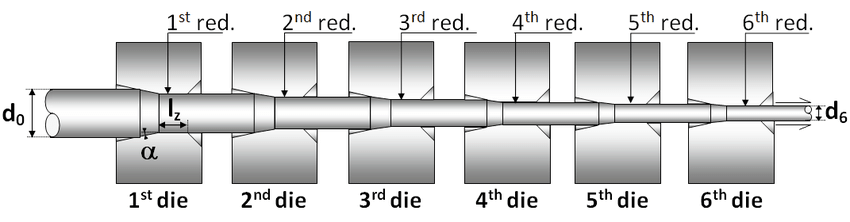
Preparation before the cold drawing
Because the hot rolled products are produced at elevated temperatures (1700 – 2200 Deg. F. i.e. hot rolling), they generally have a rough and scaled surface and may also exhibit variations in section and size. Therefore, we’d better make sure that the abrasive scale (iron oxide) on the surface of the hot rolled rough stock is removed and the surface of the bar or coil is coated with a drawing lubricant to aid cold drawing.
We should also reduce several inches of the lead ends of the bar or coil by swaging or extruding so that it can pass freely through the drawing die. Note: This is done because the die opening is always smaller than the original bar or coil section size.
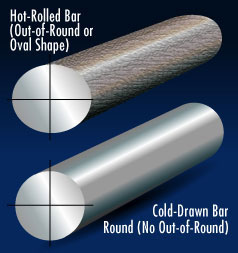
Cold drawing
In this process, the material being drawn is at room temperature (i.e. Cold-Drawn). The pointed reduced end of the bar or coil, which is smaller than the die opening, is passed through the die where it enters a gripping device of the drawing machine. The drawing machine pulls or draws the remaining unreduced section of the bar or coil through the die. The die reduces the cross-section of the original bar or coil, shapes the profile of the product, and increases the length of the original product.
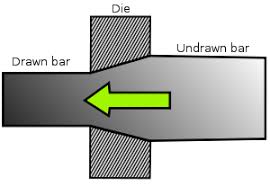
The cold drawing of complex shapes/profiles may require that each bar/coil be drawn several times in order to produce the desired shape and tolerances. This process is called multi-pass drawing and involves drawing through smaller and smaller die openings. Material is generally annealed between each drawing pass to remove cold work and to increase ductility.
Annealing
This is a thermal treatment generally used to soften the material being drawn, to modify the microstructure, the mechanical properties, and the machining characteristics of the steel, and to remove internal stresses in the product. Depending on the desired characteristics of the finished product, annealing may be used before, during (between passes), or after the cold drawing operation, depending on material requirements.
Customer Benefits of Cold Drawn Wire
- Improved Size and Section / Reduces machining losses
- Improved Steel Surface Finish / Reduces surface machining & improves quality
- Improved Straightness / Facilitates automatic bar feeding
- Increased Mechanical Properties / Can reduce the need for hardening
- Improve Machinability and Productivity / Enables higher machining feeds & speeds and improved machined finish
- Improved Formability / Improved response to spheroidization
- Improved Cost Effectiveness / Optimizes machinability and reduces yield losses