Straight Line Wire Drawing Machine
Straight Line Wire Drawing Machine is used for straight drawing without any deflection through the machine without theoretical limits as far as wire material and diameter are concerned. Presently, this machine has remarkable drawing performance for low and high carbon steel wire, stainless steel wire, special alloy steel wire, nonferrous alloy steel wire, etc.
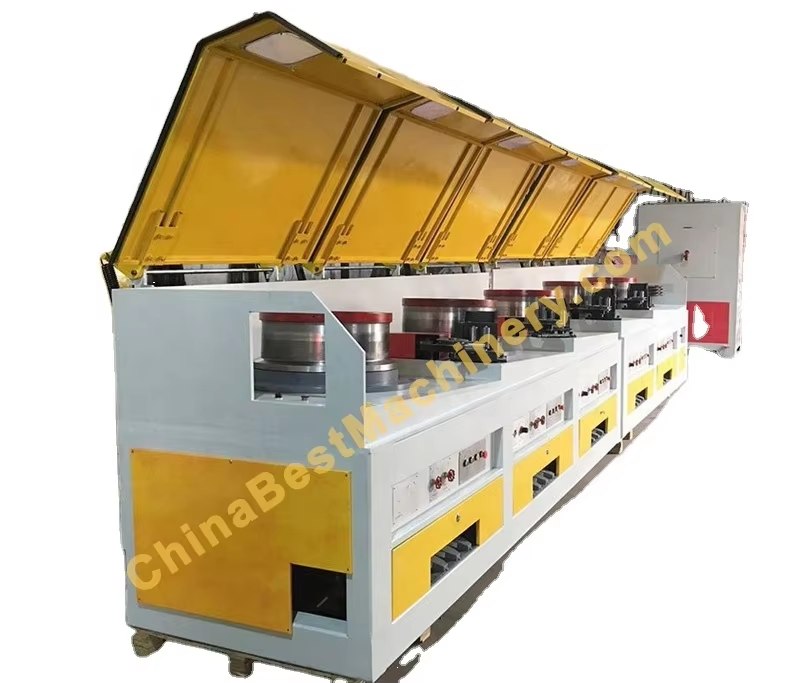
Straight Line Wire Drawing Machine Main Processes
Before starting the linear wire drawing machine, you first need to check the cooling water, drum, air pressure, and motor belt of the equipment, as well as the smoothness of the cooling water in the circulation system, and whether there is debris on the drum, etc. The main thing is whether the safety protection device is flexible enough.
According to the main drawing process, the blank wire is directly loaded onto the pay-off frame and the corresponding inspection is carried out. During the threading process, the wire must be It goes around the drum and needs to be tightened.
Before the linear wire drawing machine is officially put into operation, it needs to complete the use of the wire drawing template for a long time.
Because under normal operating conditions of the straight-in wire drawing machine, the die wall will be rubbed and washed by different wire pairs, the wear and tear on the straight-in wire drawing machine is still relatively serious. If this situation continues for a long time, over time, grooves will form where the material exits.
If the ring groove phenomenon of the draw film occurs during use, the damage to the template will be increased. If it cannot be repaired in a timely and effective manner, the loss of the operation will be greater because it cannot be repaired in time. The difficulty of repair will also increase in the future. If it continues to be severe, serious cracks will appear in the groove, and the final result will be that the mold is directly scrapped.
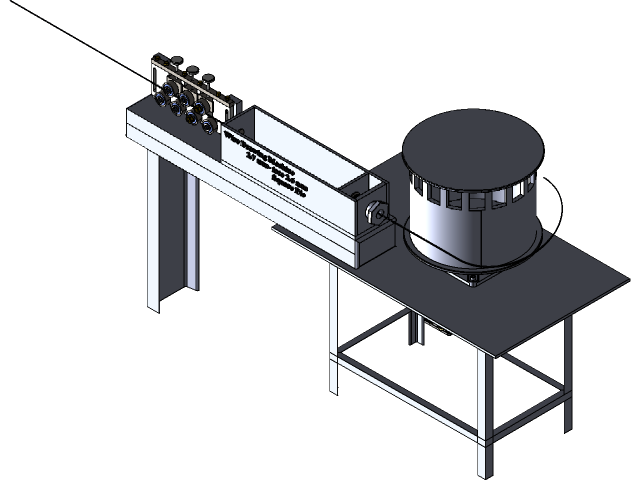
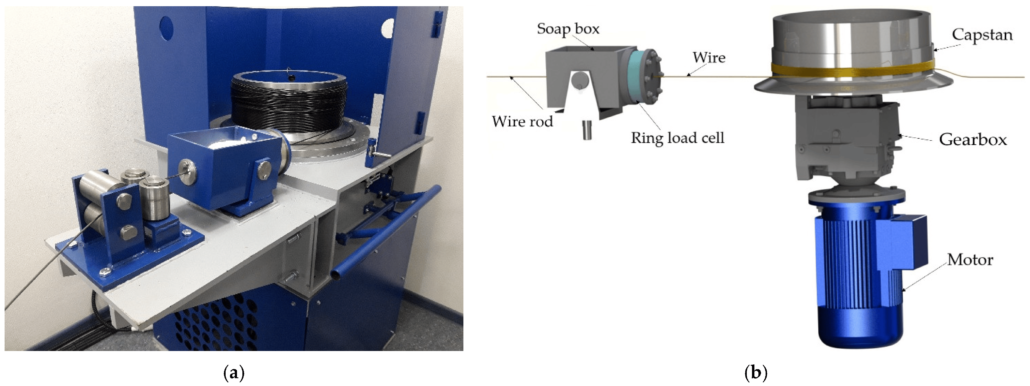
The linear wire drawing machine controls the metal flow rate per second of each drum to be equal. During the wire drawing process, the steel wire will wrap around a drum for a certain number of turns and then enter the next wire drawing die through the tuning roller.
Because of the wire drawing die Uneven wear, fluctuations in motor speed, or other reasons destroy the balance of metal flow per second, which will inevitably cause changes in steel wire tension. This change is reflected in the small-spoke swing of the tuning roller.
The displacement current sensor converts the swing displacement of the tuning roller into the electrical signal that is transmitted to the PLC through the data collection A/D board.
After calculation by the algorithm model, its output value is transmitted to the frequency converter through the data collection D/A board. The speed-given value of the frequency converter is adjusted to reach the point where the front and rear drum speeds match the intention.
The rotation speed of the product reel of the linear wire drawing machine is the pilot speed, which is the soul of controlling the speed of the entire equipment during operation.
It plays a linking role to a certain extent. The tuning roller of the product reel controls the speed of the previous reel. Speed, and then the tuning roller of the previous level of drum controls the speed of the previous level of drum, and so on.
The I-wheel take-up machine and the trunk-type take-up machine behind are also based on the speed of the product reel and use the displacement sensor of the tension control mechanism between the product reel and the I-wheel take-up machine to make the take-up machine. The take-up speed should match the finished product speed, and the flow rate per second will ultimately be the same.
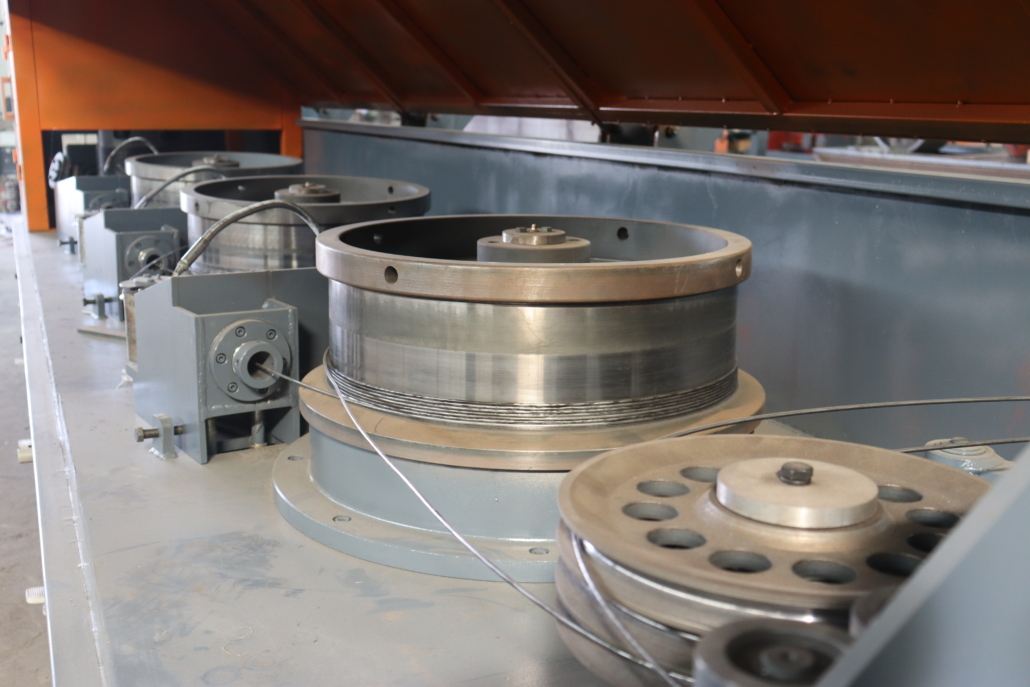
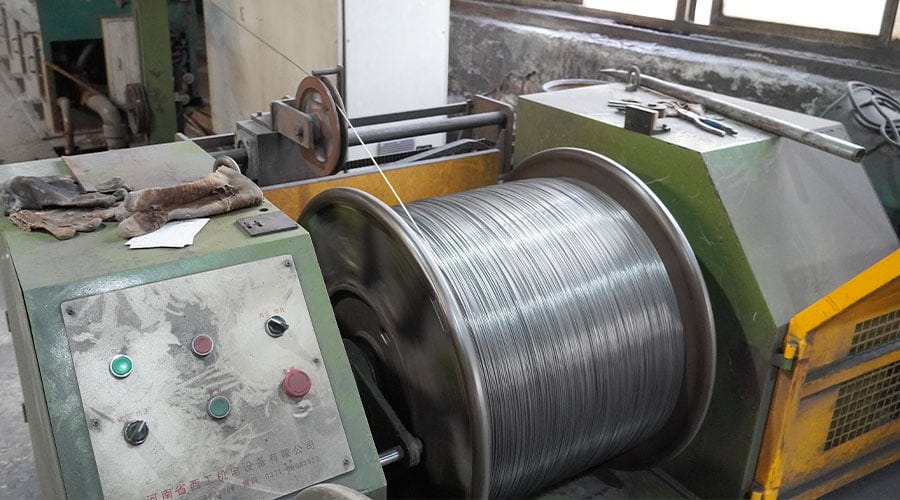
Straight Line Wire Drawing Machine Operation Precautions
- Operators must wear gloves to prevent the workpiece from burning fingers and affecting product quality.
- Before starting the machine, carefully check the air supply of the equipment and the air supply pipeline for leaks, and drain the accumulated water in the air filter.
- Install the drawing abrasive belt correctly (the direction of the arrow on the inside of the drawing abrasive belt should be consistent with the direction of the arrow on the drawing roller). Carefully check whether the upper and lower bearing seats and the lifting screw are well lubricated, and make sure there is no one on the front side of the discharging machine before starting the machine.
- After the equipment is started, you should immediately check whether the abrasive belt swing is within the required range and whether there are any other abnormalities. Otherwise, it should be adjusted or shut down immediately.
- It is strictly forbidden to start the straight-in wire drawing machines and the dust collection fan at the same time, and it is strictly forbidden for the operator to leave the workplace after starting up.
- It is strictly prohibited to place the workpiece directly on the conveyor belt without a pallet for drawing. It is strictly prohibited to place the workpiece directly on the wooden pallet without a stopper to avoid damage to the conveyor belt and the workpiece flying out and injuring people.
- When two people are working, the operator behind the equipment must not face the exit of the wire drawing machine to prevent the workpiece from flying out and injuring someone.
- The pressure adjustment of the straight-in wire drawing machines should be moderate. Under normal circumstances, the pressure gauge indication should be between 35 and 75. It is strictly forbidden to exceed the red line to avoid causing equipment or personal accidents.
- It is strictly prohibited to adjust the air pressure when the equipment is in normal operation to prevent the abrasive belt from losing control and causing equipment and personal accidents.
- If an abnormality occurs during the operation of the wire drawing machine, it should be shut down immediately and the power should be cut off to avoid the expansion of the fault.
- During maintenance of the straight-in wire drawing machines, the main power supply should be turned off and a sign indicating that operation is strictly prohibited to avoid accidents.
- When leaving work or when the equipment is not used for a long time, the main power supply and compressed air should be turned off to ensure the safety of the equipment.