what is wire drawing
what is wire drawing
The wire drawing is a metalworking process used to reduce the cross-section of a wire by pulling the wire through a single, or series, of drawing die(s). The wire is prepared by shrinking the beginning of it, by hammering, filing, and rolling, so that it will fit through the die; the wire is then pulled through the die. As the wire is pulled through the die, the volume remains the same, so as the diameter decreases, the length increases.
Wire drawing is a metalworking process used to reduce the cross-section of a wire by pulling the wire through one or more dies. There are many applications for wire drawing, including electrical
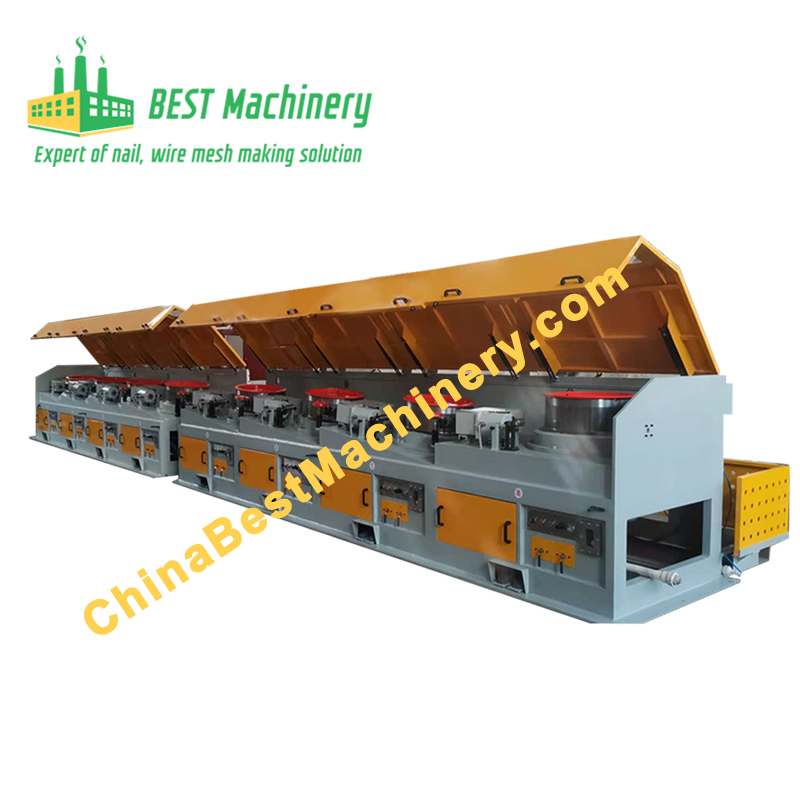
wiring, cables, tension-loaded structural components, springs, paper clips, spokes for wheels, and stringed musical instruments. Although similar in process, drawing is different from extrusion, because in drawing the wire is pulled, rather than pushed, through the die. Drawing is usually performed at room temperature, thus classified as a cold working process, but it may be performed at elevated temperatures for large wires to reduce forces.
The wire drawing process is quite simple in concept. The wire is prepared by shrinking the beginning of it, by hammering, filing, rolling or swaging, so that it will fit through the die; the wire is then pulled through the die. As the wire is pulled through the die, its volume remains the same, so as the diameter decreases, the length increases. Usually, the wire will require more than one draw, through successively smaller dies, to reach the desired size. The American wire gauge scale is based on this. This can be done on a small scale with a draw plate, or on a large commercial scale using automated machinery. The process of wire drawing changes material properties due to cold working.
What is Stainless Steel Wire Drawing
Stainless steel wire drawing offers numerous benefits that make it an attractive choice for different industries. One of the most important advantages is its high corrosion resistance, which makes it suitable for harsh environments and applications where hygiene is crucial, such as in medical equipment and food processing machinery.
Another key benefit of stainless steel wire drawing is its strength and durability. The material can withstand heavy loads and stress without deformation or breakage, making it ideal for use in structures, cables, springs, and other components that require toughness.
In addition to these advantages, stainless steel wire drawing also provides excellent aesthetic appeal with a highly polished surface finish that enhances the appearance of products. It’s also easy to clean and maintain due to its non-porous surface.
The key phrase “wire drawing dies” plays an important role in determining the final quality of the product as it helps maintain consistency during wire reduction. These are typically made from tungsten carbide which provides excellent wear resistance.
Another important key phrase is lubrication, which is critical for ensuring smooth and efficient wire drawing operation while also preventing corrosion or rusting issues that arise due to exposure to heat or moisture during processing.
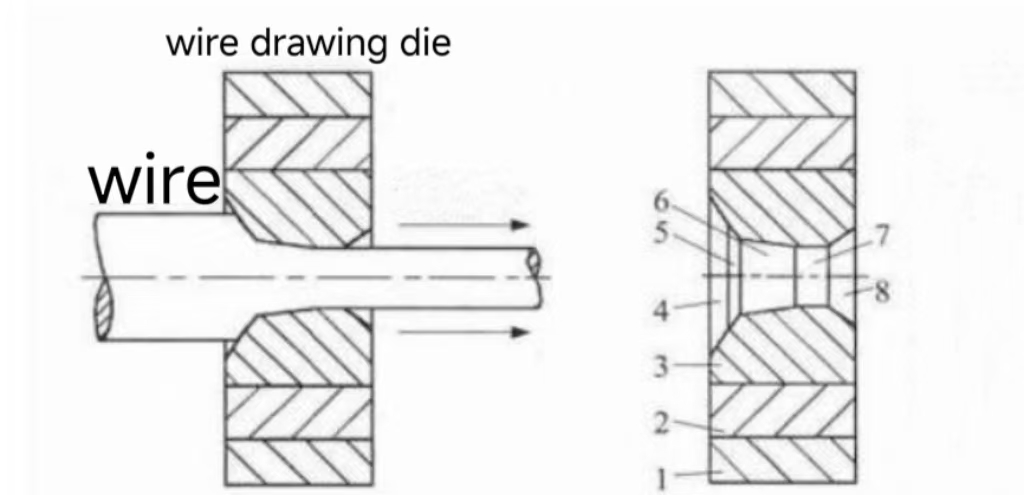
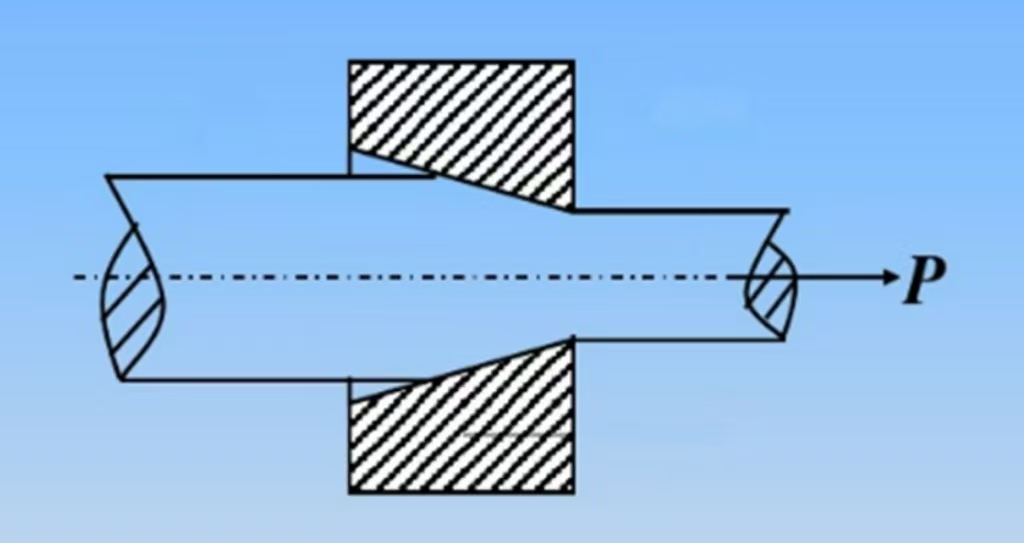
Wire Drawing Process
1. Install the drawplate: To provide necessary leverage, the drawplate must be secured in a bench vise that has been mounted to a fixed work surface (a drawbench specifically designed for this task can also be used). Secure the drawplate in the vise, placing a piece of copper or other soft metal over the jaws of the vise to protect the drawplate. Be careful not to clamp over any hole openings.
2. Taper the wire: In order to insert your wire into the drawplate, the first 1 to 2 inches of the wire must be tapered. This taper can be achieved through one of the following methods:
- Using a flat file: File the end of the wire to a taper. The taper need not come to a point.
- Using a hammer: Hammer the end of the wire, while rotating it with your fingers, to reduce the diameter. It may be necessary to anneal the wire if it becomes work-hardened during hammering.
- Using a rolling mill: If you have a rolling mill with wire rollers, this is the quickest method to produce a taper on your wire. Adjust the distance between the rollers so that they almost touch (never let the rollers touch during operation). Select an opening that is slightly smaller than the diameter of your wire. Roll the wire through approximately 2 inches. Reverse the direction of the rollers to remove the wire, rotate the wire 90˚, and roll it again to the same length. Move to the next smallest opening and repeat the process, rolling the wire 11/2” through the mill. Finally, repeat a third time, rolling 1” through the mill. You should end up with a stepped taper. If desired, the steps can be removed by hammering the wire lightly while rotating.
3. Anneal the wire: Using a torch, anneal your wire, then pickle to remove any oxidation. This will help prevent the wire from breaking during the drawing process.
4. Lubricate the wire: Coat your wire completely with beeswax, paraffin, or Bur Lube (item 330-060).
5. Pull-through drawplate: Select a hole in the drawplate that is slightly smaller than the diameter (not the taper) of your wire. Insert the tapered end of your wire into the back (unmarked side) of the drawplate. Grasp the wire from the front of the plate with a drawtong or heavy-duty pliers and slowly pull the wire through the plate. Maintain a constant speed to ensure uniformity. Repeat this process with successively smaller holes until the desired diameter is achieved. If the wire becomes tough and springy, it should be annealed, cleaned, and re-lubricated. It may also be necessary to re-taper the end of the wire after successive passes.