Automatic Wire Drawing Machine Wire Breakage
The automatic wire drawing machine is a piece of equipment specially designed for wire drawing processing of stainless steel surfaces. It is suitable for surface wire drawing processing of circular, cylindrical, flat plates, chassis, cabinets, mobile phone cases, tableware, kitchen utensils, and other stainless steel products. But for some reason, wire breakage sometimes happens.
Functions of The Automatic Wire Drawing Machine
Automatic wire drawing machine is often used in daily life, meeting the high standard requirements for processing methods in modern life, and are widely used in daily production and processing.
The automatic wire drawing machine is a kind of mechanical equipment widely used in workpiece processing. It is also a large piece of equipment required by customers for wire drawing processing. However, there is relatively little understanding of the automatic wire drawing machine.
Understanding the functions of the automatic wire drawing machine will help manufacturers to produce efficiently and produce good quality products. So, what are the functions of the automatic wire drawing machine?
The functions of the automatic wire drawing machine are divided into six points:
- It is firmly adsorbed on the surface of the steel wire and enters the drawing die with the steel wire, effectively separating the two interfaces in the deformation zone;
- Resistant to high pressure and high temperature. Under the high pressure and temperature rise conditions that occur during drawing, the smooth film can still maintain its continuity and lubricity without being damaged, coking, agglomerating, or deteriorating, that is, it has physical and chemical properties. stability;
- The automatic wire drawing machine has excellent extensibility and lubricity, that is, it can not only be firmly adsorbed on the surface of the steel wire but also extend and deform along with the steel wire. The smooth film has a layered structure, and the molecular binding force within each layer is strong. The intermolecular binding force is weak;
- The components that make up the lubricant will not react chemically with the steel wire matrix, produce compounds that affect the performance of the steel wire, or have a corrosive effect on the steel wire, and are easy to remove.
- The drawing effect of the automatic wire drawing machine can increase the textured beauty and beautiful lines of the stainless steel surface, and remove impurities, scratches, bruises, etc. on the stainless steel surface.
- It has the characteristics of automated control, reducing labor costs, improving production efficiency, and making it easy and fast to disassemble and install abrasive belt consumables.
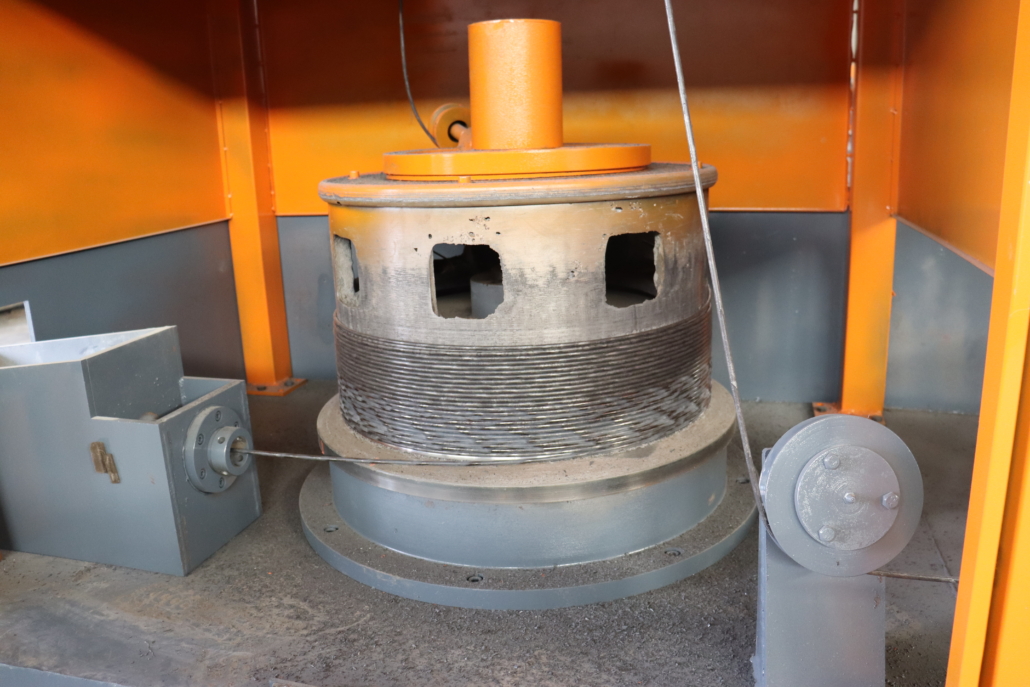
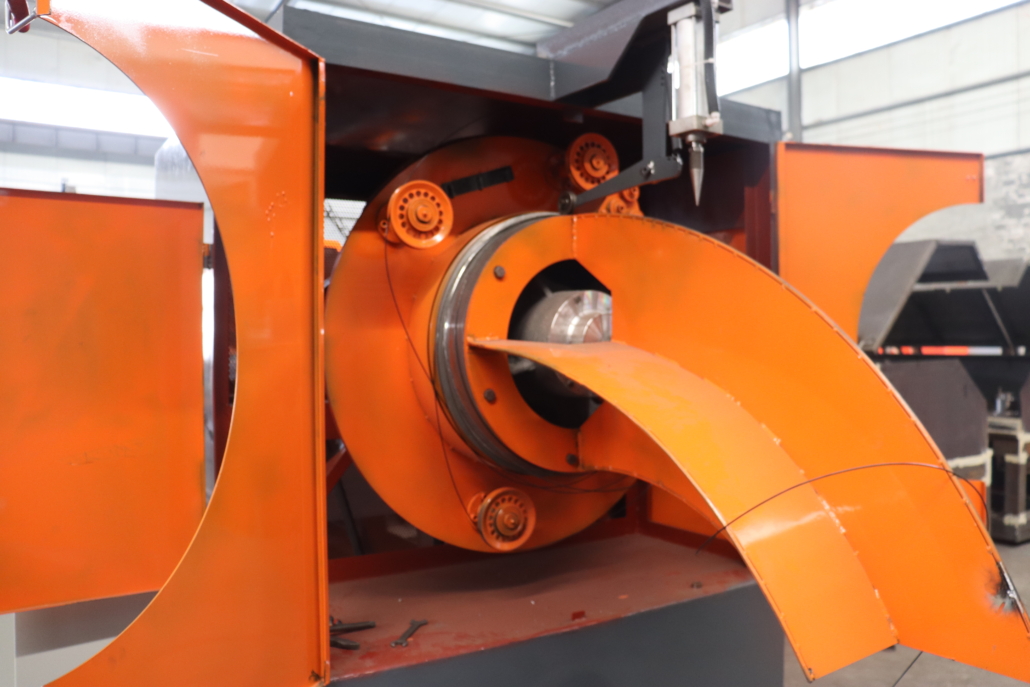
Our technicians who have used wire drawing machines all know that wire breakage during work is a common problem with automatic wire drawing machines. We will analyze the reasons for wire breakage in automatic wire drawing machines and find solutions together:
Reasons For Wire Breakage In Automatic Wire Drawing Machine
- During uninterrupted production, the sizing area of the wire drawing die will become larger due to normal wear and tear, causing wire breakage.
- Due to the instability of the annealing current during production, the current suddenly becomes high, and the monofilament is pulled off during the annealing process or fused by the sudden strong current.
- The quality problems of various rod materials cause wire breakage. The rod material has irregular quality defects, which causes the monofilament to be broken by various unpredictable tensions during wire drawing deformation.
- The cone wheel of the copper wire drawing machine is grooved or has too many windings, causing wire pressure.
- The joint is not firm.
Solutions To Wire Breakage In Automatic Wire Drawing Machine
- Check the wire drawing machine equipment before production and processing, and replace the wire drawing die.
- Check the power supply to ensure that the current and voltage are stable.
- Select different mold matching plans according to different pole materials and continue to explore them during production. It is necessary to conduct sufficient self-inspection on the rods to be produced, promptly discover the quality defects of the rods, and find corresponding countermeasures in time according to different situations, reduce the drawing speed, or remove the defective sections.
- Pay attention to the operation method and replace the cone wheel.
- Ensure joint quality.
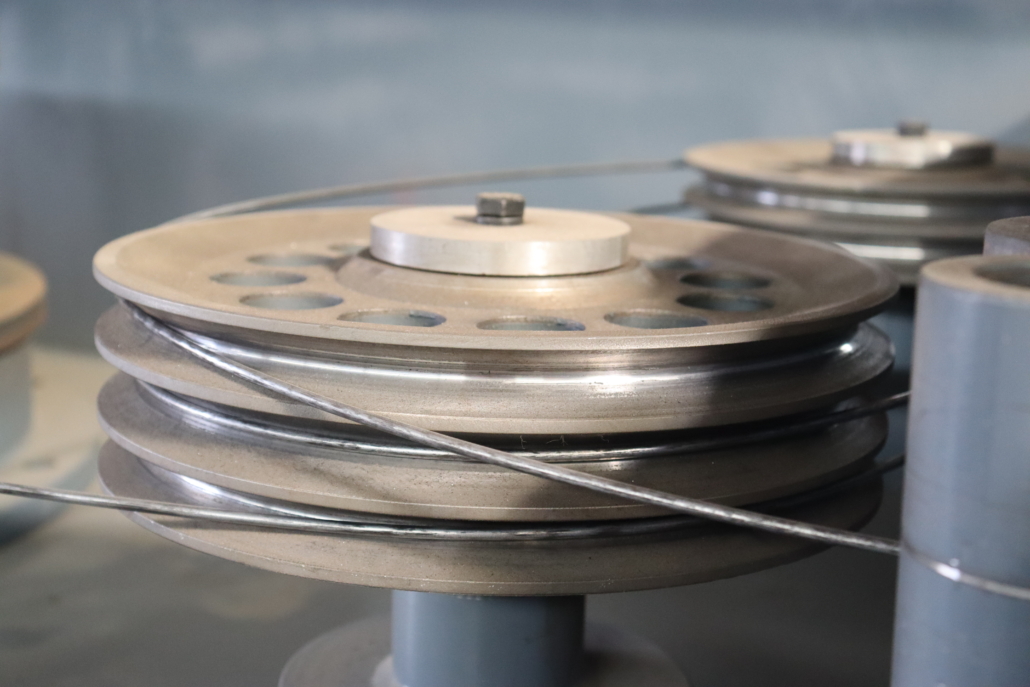
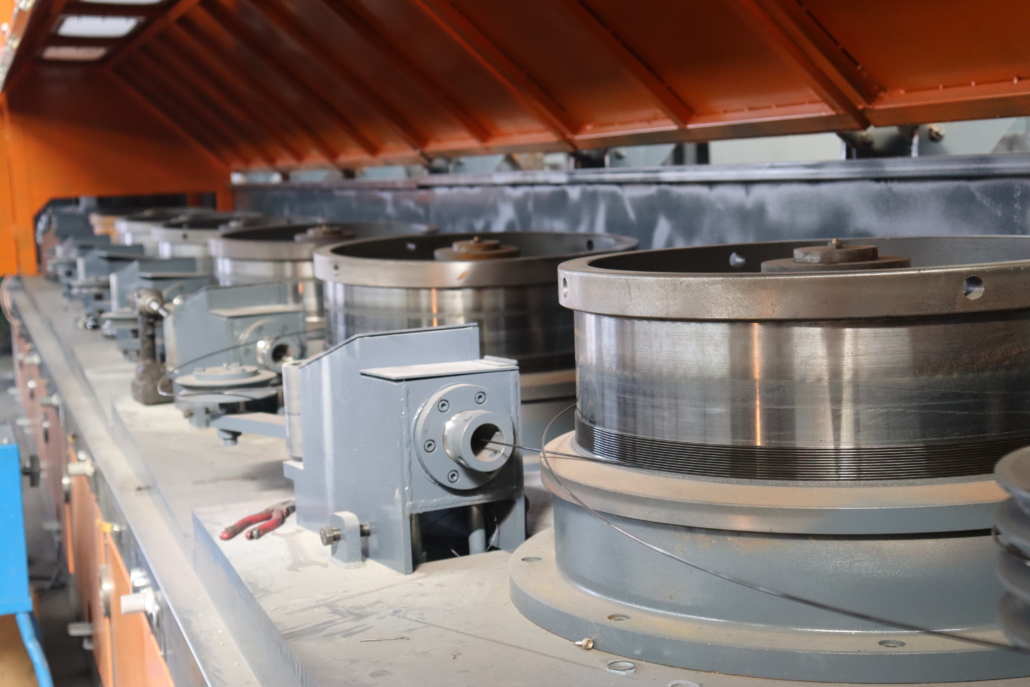