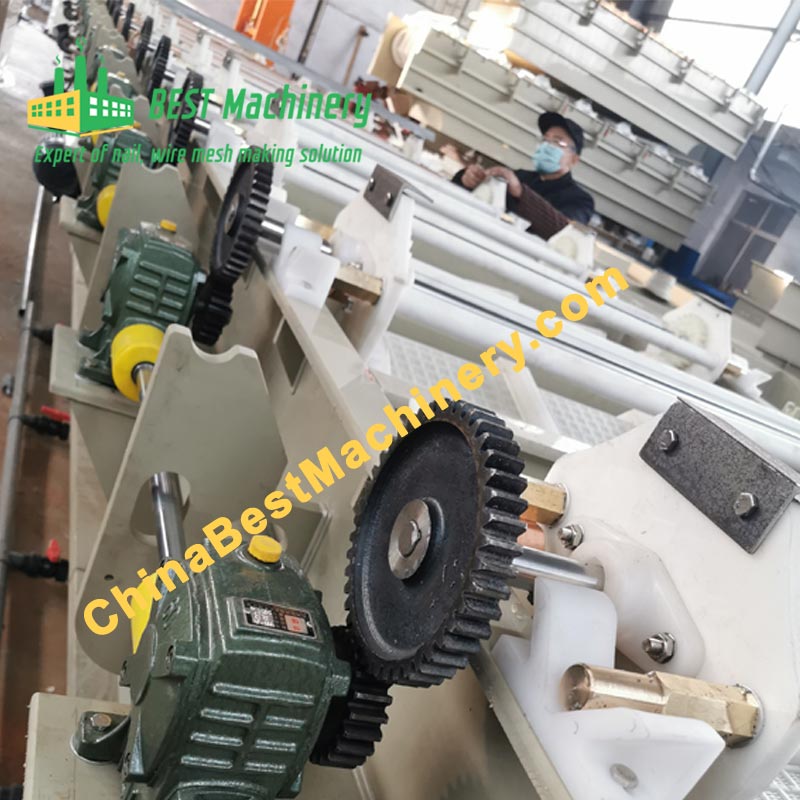
- Usage: Galvanized roofing nails
- Output: 120kg/Hour, customized accepted
- Drums: 4+4+4+4, customized accepted
The purpose of the Continuous Galvanizing Line (CGL) is to apply a coat of zinc onto the surface of steel sheets or roofing nails in an effort to increase their corrosion resistance. There is a wide range of control of zinc coat thickness, and the galvanized steel sheets are used for a broad range of purposes, including construction materials, automobiles, and electrical appliances. Steel Plantech’s CGLs possess unsurpassed functions that are highly evaluated by customers around the world.
Product Quality Improvement
High-quality galvanized steel strips for use in automobiles can be produced through the use of air knife and highly precise zinc coating weight gauge. That quality is attested to by our track record of supply to many customers around the world.
How to design a galvanizing process line with customer requirements?
For we could design a suitable machine for you. there are some questions as below:
- It’s the first time you to do a plant?
- What are the products you want to galvanize, any pictures?
- What do you want to plate? Zinc? Nickel? copper or other?
- The product size? smallest one size?
- Largest one size?
- How much does a single product weigh?
- The product’s raw material?
- How many do you want to plate one day? (8 hours working)And also there is some standard information sharing with you here.
- Item: Electroplating equipment ( The whole electroplating production line )
- Services: For plating products with Iron, SS, Low-carbon steel, plastic
- Coating type: Zinc, Nickel, Silver, Gold, Chrome, ABS plating, copper, Tin, etc
- Type: Hang plating / Barrel plating Accessories: PP Tank, PP barrel, Crane lifting, hanger, rectifier, chemical solution etc.
- After-sales Service Provided: Yes Voltage: 380V ( Welcome Customized )
- Model Number: Depends on your actual plating products.
- Lead time: 30-35 working days after prepaid
What is the process flow of galvanization:
oil and rust removing—washing —galvanizing–washing—polishing–washing—surface passivation—hot washing– drying–packaging.
- oil and rust removing— By Dipping in the ACID drum MANUALLY, or putting in the process line by 4 drums,
- washing— BY Dipping in a WATER drum Manually
- galvanizing— BY putting in galvanization equipment
- washing— AFTER discharge from the galvanizing machine, then DIPPING into water drums.
- polishing— put the nails into brightener liquid to polish for several seconds.
- washing— wash again by DIPPING into WATER DRUM
- surface passivation—put the nails into passivation liquid for several seconds
- hot washing—put the nails into hot water for washing.
- drying— By putting nails into a centrifugal dryer machine.
- packaging— By carton or bags.
Galvanizing chemicals:
The chemical liquid for galvanizing is non-toxic and has no smell and is easy to get it locally, such as potassium chloride, KCL, Zinc Ingot, boracic acid, and some common chemical powders. According to a certain proportion, mix it with water.