Wire Drawing Manufacturing Process
Tube & Wire Drawing Manufacturing Process
Wire Drawing
The wire drawing manufacturing process of wire drawing involves the production of wire of close diameter and tolerance by drawing a descaled hot-rolled rod through a die. The finished wire is coiled onto a motor-driven block. The dies are manufactured from hard material e.g. tungsten carbide. Diamond dies are used for small-diameter wire. Soap is used for lubrication. If large diameter reductions are required the rod is progressively drawn through several stages of dies and blocks.
Wire can be extruded at speeds of up to 2000m/min.

Steel Tube Manufacture
Most ferrous seamless tubes are first rotary forged. This wire drawing manufacturing process consists of two hot working processes the first of which is rotary piercing.
In rotary piercing a rolling mill consisting of two rolls set at an angle to each other is used- see the figure above. A metal billet is fed into the rolls which simultaneously rotate and draw the billet forward. Because of the small diameter of the rolls the outside of the billet is deformed resulting in a tensile stress at its centre. A cavity is induced in the center of the billet, the formation of which is assisted and controlled by a profiled mandrel. The type of rolling mill shown in the figure is the Mannesmann mill.
The extreme deformations resulting from the wire drawing manufacturing process can result in faults unless a high-quality material is used. The material must remain ductile over a wide temperature range.
Rolling mills based on three rolls have been developed which are more tolerant of material quality.
The second stage in producing seamless steel tubes is to locate the rough tube onto a mandrel and roll it to reduce its wall thickness. A Pilger mill is one which can be used for this wire drawing manufacturing process. The roll arrangement and process are shown in the figure below.
A heated tube is reciprocated under cam-shaped rolls. First, the tube is moved forward under the rolls. The profiles of the rolls are shaped so that on rotation they bite into the tube to force it down onto the mandrel. The mandrel is then moved back to drag the tube against the rolls and smooth its outside diameter. The cycle is repeated.
Tube drawing
If cold drawn seamless tubing is require with small diameters, thin walls, or a smooth surface finish then the tubes manufacturing process is completed using cold drawing.
Prior to cold drawing, the scale resulting from rotary forging is removed by pickling.
A draw bench is used to pull the tube through a drawing die. One end of the tube to be drawn is collapsed and fed through the die. This end is then clamped to a traveling carriage. The carriage is then moved away from the die using either mechanical or hydraulic traction. In practice, several tubes may be drawn in parallel to increase productivity.
A number of process options are available as shown in the figure below.
The simplest option sinking is the least accurate. Using a plug or/and mandrel results in more accurate tubes but more energy is required for the wire drawing manufacturing process.
Lubrication is vital for this process to reduce friction and to reduce metal transfer from the tube to the die.
The die can be made from alloy steel but more often the die is made from tungsten carbide or from other more exotic variants.
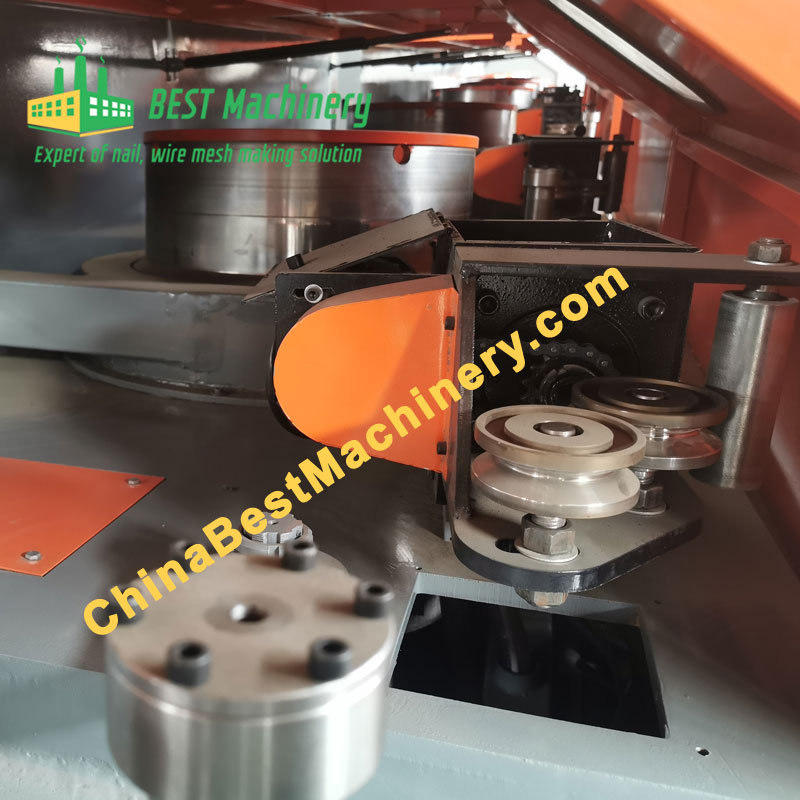
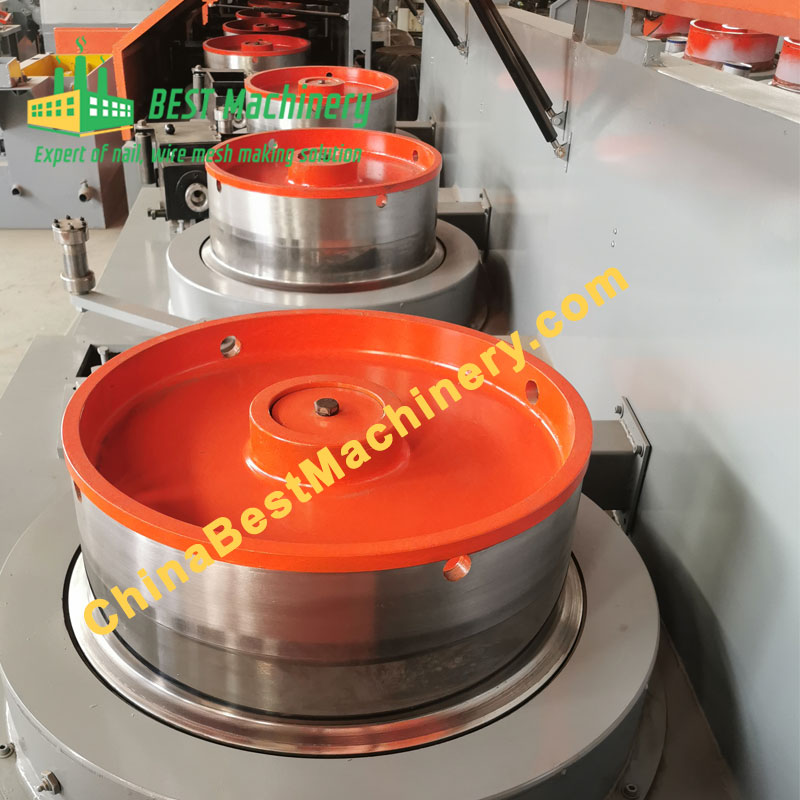
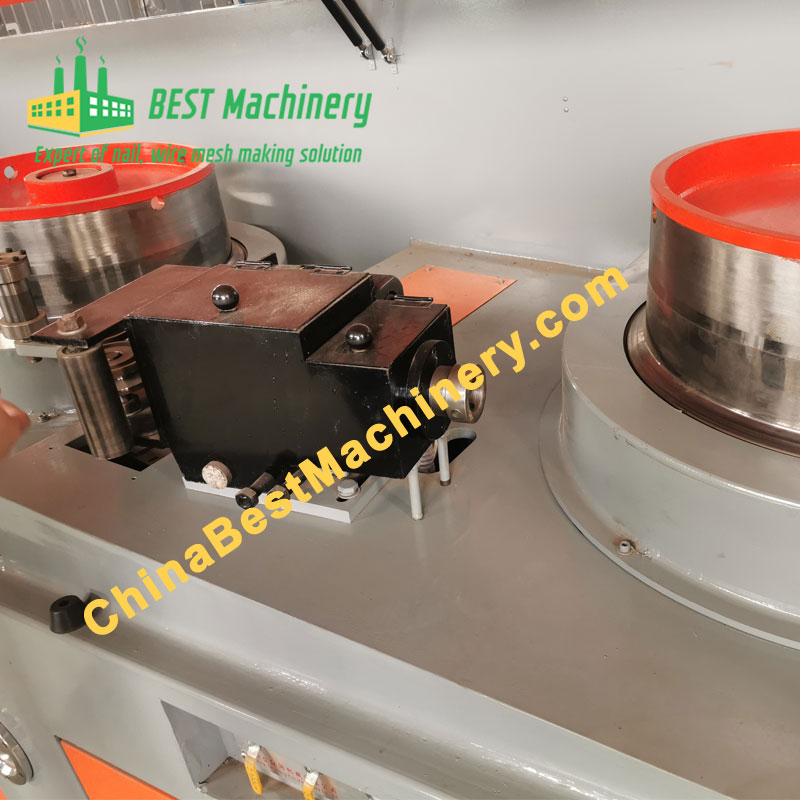
Cold-Drawn Steel Wire Manufacturing Process
Cold drawing changes the steel’s shape and size by pulling the material through a carbide die or Turks’ head. Often, steel will go through cold-rolling first and then cold-drawing to enhance its properties for better performance.
At Best, we have single-die, multi-die, and Turks head capabilities. This variety lets us create cold-drawn steel to your exact specifications. Plus, our process creates minimal scrap, and the cost is lower than it would be to complete the necessary machining yourself.
Benefits of Cold-drawn Steel Wire
Cold drawing has several benefits compared to other methods such as hot-rolling, including:
- Precision: This process can work within closer size and roundness tolerances than other methods. Where hot-formed steel products will warp during cooling, cold-finished steel maintains its precise shape. We can create sharp corner radii down to 0.127 millimeters or 0.005 inches, as well as complex symmetrical and asymmetrical profiles.
- Performance: Cold-drawn steel has enhanced mechanical properties. This transformation process has a positive effect on tensile and yield strength and reduces ductility, which makes better performance possible. After undergoing this process, steel is stronger and harder.
- Surface finish: A smoother surface finish can be used for various applications and eliminates additional machining operations and costs.
- Machinability: Cold-finishing enhances machinability, especially with low-carbon steel, and lengthens tool life.
When you choose to source cold-drawn products from Best, your company will benefit from:
- Several capabilities: Best has single-die, multi-die, and Turks head capabilities under one roof.
- Cost savings: Cold-finishing is more cost-effective than machining the part yourself.
- Less waste: Cold drawing produces minimal scrap, eliminating the waste of purchased steel stock.
The Process of Making Cold-Drawn Steel Wire
Best uses industry-leading processes to create cold-drawn products for our customers. The cold-drawn steel manufacturing process starts with room-temperature hot-rolled steel stock in wire form. We begin by removing the iron oxide layer on the surface to improve dimensional control and remove superficial imperfections, then lubricate the steel wire for the next step.
Then, we use a powered capstan attached to the steel stock to draw the wire through a carbide die or turks head. Each pass through the die reduces the wire’s diameter, elongates the steel wire, and alters its shape within a tight tolerance. Extra dies can reduce the diameter even further.
We can draw the wire through the die several times to reach your desired dimensions. The result of the cold-drawing process is a thin rod or wire shape. Once we have the finished product, we wind the cold-drawn wire to your packaging requirements.
Another process we use involves cold-rolling the steel rod to roughly shape the stock. Then, we finish the rod with cold-drawing to enhance the steel’s properties and performance. Our in-house metallurgists and engineers can advise you on which steel stock and cold-drawn processes are the best for your application.