The Coil Nail Production
What is the coil nail production line
The coil nail production line refers to the process of manufacturing coil nails using a range of different machines, including wire drawing machine, nail making machine, nail polishing machine, thread rolling machine, and coil nail making machine. Coil nail is arranged in a circle connected together by a copper-coated iron wire. There are four main shapes, including small, big, jumbo and conical coil nail. The main types of coil nails are smooth shank coil nail, ring shank coil nail and screw shank coil nail. It is placed in a nail gun to punch into wood or pallet and is often used in furniture assembling, timber frame construction, wire reel making and wood pallet, crate and packing.
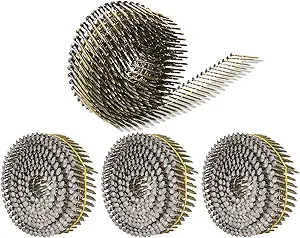
What are the machines of the coil nail production line
There are mainly five machines in manufacturing the coil nail, including a wire drawing machine, nail making machine, nail polishing machine, thread rolling machine and coil nail making machine. The wire drawing machine reduces the diameter of steel wire to the desired size. The nail making machine cuts the wire into lengths, makes the nail head, and sharpens the point. The nail polishing machine makes nails smooth and bright. The thread rolling machine forms different types of nails. The coil nail making machine uses the copper-coated welding wire to weld the threaded nails and rolls them in a coil.
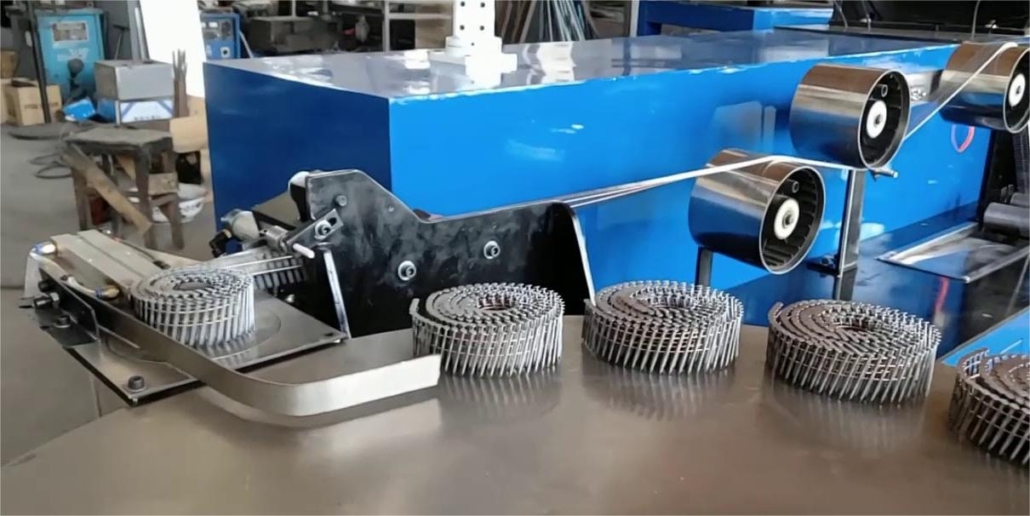
How to manufacture coil nails
The coil nail production process can be divided into six steps:
Wire Drawing
The production process begins with wire drawing. The 6.5mm steel wire is drawn by the wire drawing machine to small diameter wire rod like 2.8mm, 3.1mm, 3.4mm, 3.7mm, 4.1mm and 4.5 mm so that they can be feed into the nail making machines. By changing different drawing dies, you can get any diameter you need for making nails. And using the drawing powder can reduce the friction between the steel wire and the drawing die and prolong the service life of the drawing die.
Nail Making
The drawn wire is then fed into the nail making machine, which cuts the wire into the desired lengths, forms the nail head by using the pin punch, and sharpens the nail tip with the nail cutter. The different nail length is determined by the length delivered by the nail box. The nail making machine runs at a high speed and can produce a large amount of nails in a short time. Those quick-wear parts, such as nail cutter, nail die and pin punch, need to be replaced in time to ensure the production of high-quality nails.
Nail Polishing
Following the nail making process, the semi-finished nails go through a polishing stage. The nail polishing machine is to polish the nails with saw dust, engine oil, paraffin or other materials to remove any burrs or imperfections on the nails. Saw dust removes any sharp edges, engine oil is used to brighten wire nails and give a shiny surface, and paraffin increases the rust resistance of wire nails. Therefore, the finished wire nails are bright and have a very smooth surface.
Thread Rolling
After polishing, the wire nails are threaded by the thread rolling machine, which is used to make screw shank, ring shank and spiral shank nails by adopting a cold working technology. The thread rolling machine is equipped with a vibration plate. Wire nails are placed in the vibration plate and then automatically ordered in a roll. Finally, wire nails go through different thread rolling molds to form different screws. Notably, the process does not wear out the wires. If making smooth shank coil nails, there is no step of thread rolling.
Coil Nail Making
The threaded nails are then formed the coil nail by the coil nail making machine. The working principle of the coil nail making machine includes five parts. Firstly, put the threaded nails in the vibrating plate, then the messy nails will be arranged in order by the vibrating plate. Secondly, the nails drop to the welding wheel through guide and are welded by the copper coated welding wire into the wire row nails. Thirdly, the wire row nails automatically pass the oil box and counting device and roll in coil. Fourthly, the machine will cut automatically after the nail quantity reaches the set nail quantity. Finally, the operator adds the rubber band to the finished coil nails. Coil nails are advantageous for many applications because they can be easily and quickly loaded into nail guns or other automated.
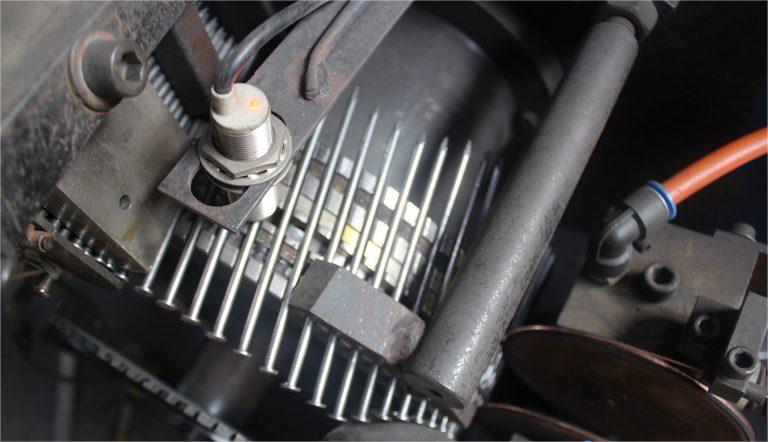
Quality Control and Packaging
The final step in the process is quality control and packaging. The finished coil nails are inspected to ensure they meet all quality standards. The quality inspection can be done manually or with automated machinery. Once the coil nails pass the quality inspection, they are packaged in cartons. Every carton can contain twenty coil nails.
It’s worth noting that the precise details of this process may vary depending on the specific equipment, quality standards, and exact types of coiled nails they produce.
The Quick-Wear Parts in the Production of Coil Nail
To produce high-quality coil nails, it is important to regularly maintain and inspect all parts of the coil nail production line, especially those quick-wear parts. Timely detection and resolution of wear pieces also minimize downtime and keep production lines running smoothly. The following are the most common wearing parts on the coil nail production line:
- Wire drawing die. The wire drawing die reduce the steel wire to the desired diameter in wire drawing process. And the die can wear out in the wire drawing machine over time due to the continuous friction with the metal wire.
- Nail cutter. The nail cutter is used to cut the cold drawn wire to wire nails in nail making stage. Due to the continuous cutting process in the nail making machine, the knives become dull and require replacement to maintain the quality of the cut.
- Nail mold. Also, the nail mold is designed to grip the drawn wire when punching and can wear out because of the constant operation of nail making machine and requires periodic replacement.
- PinPunch. The pin punch forms the nail head in the nail making machine. The constant impact can cause it to wear out or break, so the punch bar requires prompt replacement.
Failures and Solution of Coil Nail Machine
During long-term operation, various failures may occur in the coil nail making machine. Understanding common failures and their troubleshooting methods is essential to ensure the normal operation of the coil nail machine and extend its life. The following are some common failures of nail coiling machines and their troubleshooting methods:
Fail to start the machine under normal jog
- Check the touch screen log bar for fault prompts and solve them according to the prompts.
- Is the emergency stop pressed? If it is pressed, please pop it up.
Fail to cut off the coil nails
- The cutter cuts on the nail, moving the cutter left and right to ensure that it cuts between two nails.
- The direction of the cutter is consistent with the direction of the coil nail.
Nail stuck in guide rail outlet
- The nail specifications must be uniform, and there must be no curved nails or nails of different sizes.
- The size of the nail-bearing wheel matches the nail, and the standard is that the nail is just put into the wheel without popping out.
- The magnet is placed in the middle of the guide rail gap, and the magnet frame cannot be higher than the nail-bearing wheel groove.
- The gap between the nail-bearing wheel and the guide rail is between 0.5mm and 1mm.
- The nail tip is too large in diameter, causing the nail to be stuck, which is generally caused by the old thread rolling machine mold damage.
- The entire guide rail outlet angle should be the same as the nail wheel groove angle (adjusted at the factory).
- Note: You can slow down the device and carefully observe which part is causing the jam, and then solve it accordingly.
I hope this information is helpful, and if you have any further questions about coil nail making machines, feel free to ask!
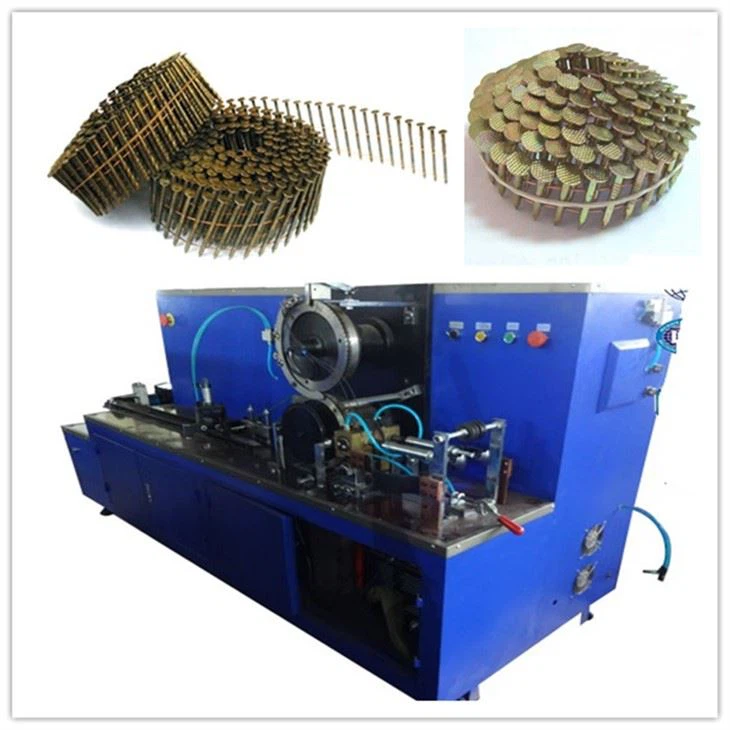